Clear Plastic Injection Molding
Need Clear Plastic Injection Molding Services?
Make Sure You Contact Us!
At Bosworth Plastics, we are proud to offer high-quality clear plastic injection molding services tailored to the diverse needs of various sectors, such as medical devices, automotive, consumer electronics, and aerospace, where clarity, precision, and aesthetic appeal are paramount.
Clear plastic injection molding is distinct from traditional molding processes due to the unique challenges it presents. The production of clear plastic parts requires a deep understanding of materials, advanced Mold design, and precise control over the manufacturing process.
At Bosworth Plastics, we have honed our expertise in this complex area, ensuring that our clients receive the highest quality products to meet their exact specifications!
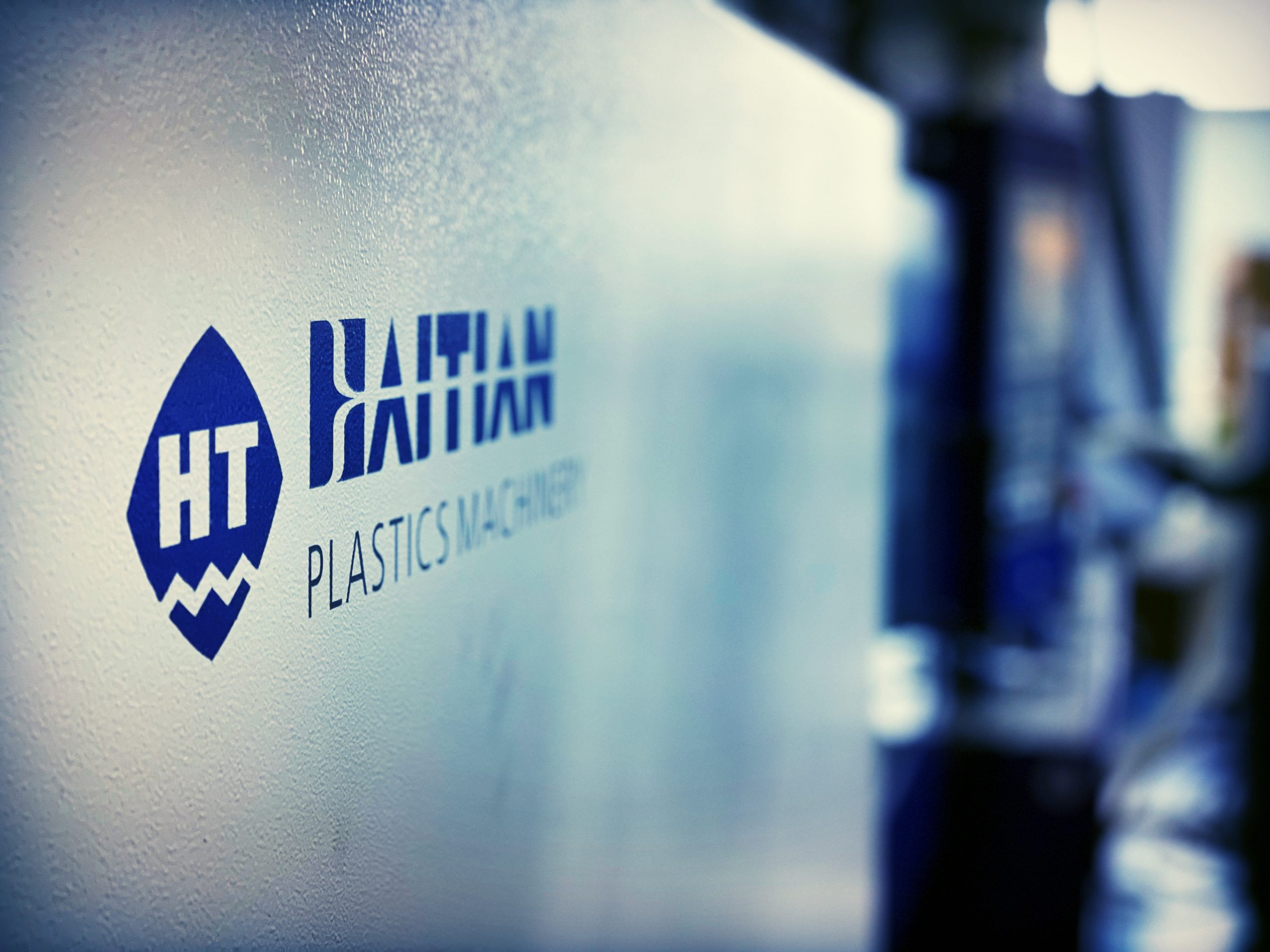
The Clear Plastic Injection Molding Process
Producing clear plastic components involves more than just selecting a transparent material and molding it into shape.
The clarity of the final product is influenced by numerous factors, including the material’s purity, the design of the Mold, the molding process parameters, and post-production treatments.
Each step in the process must be meticulously managed to avoid defects such as cloudiness, bubbles, and surface imperfections that can compromise the clarity and performance of the final product.
Material Selection And Purity
The choice of material is paramount when creating clear plastic products. Common materials used include polycarbonate (PC), acrylic (PMMA), and polyethylene terephthalate glycol (PETG), each offering different properties in terms of clarity, strength, and flexibility.
For example, polycarbonate is known for its high impact resistance and durability, making it ideal for safety goggles, automotive components, and lighting covers. Acrylic, on the other hand, offers excellent optical clarity and UV resistance, which is essential for products like lenses and display screens.
PETG is another popular choice for its ease of processing and versatility, often used in medical devices and food packaging.
The material used must be of the highest purity to achieve optimal clarity. Any impurities or contaminants in the material can lead to defects in the final product, such as haze or discolouration.
That’s why at Bosworth Plastics, we ensure that all materials used in our clear plastic injection molding processes are sourced from reputable suppliers and meet stringent quality standards.
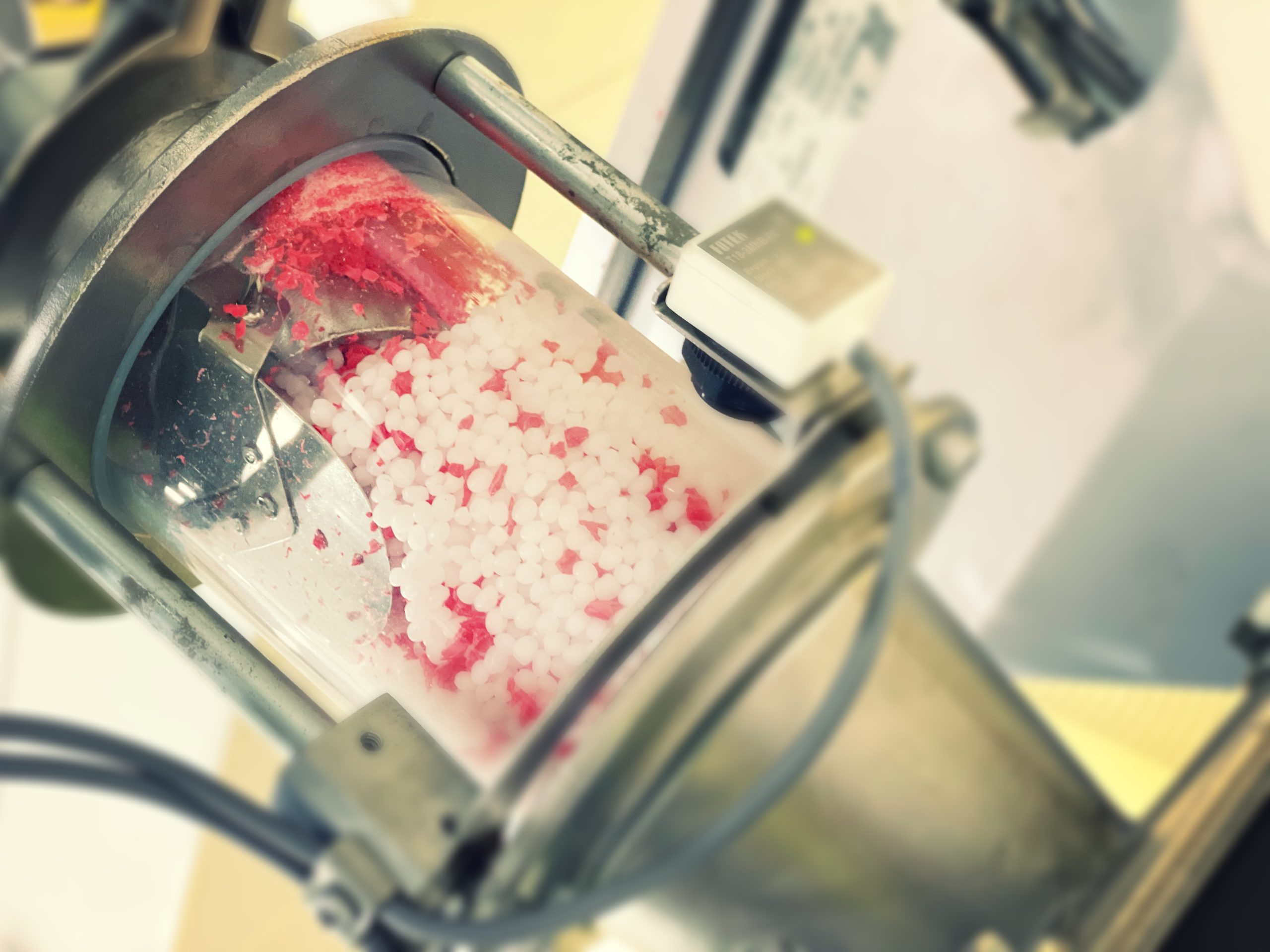
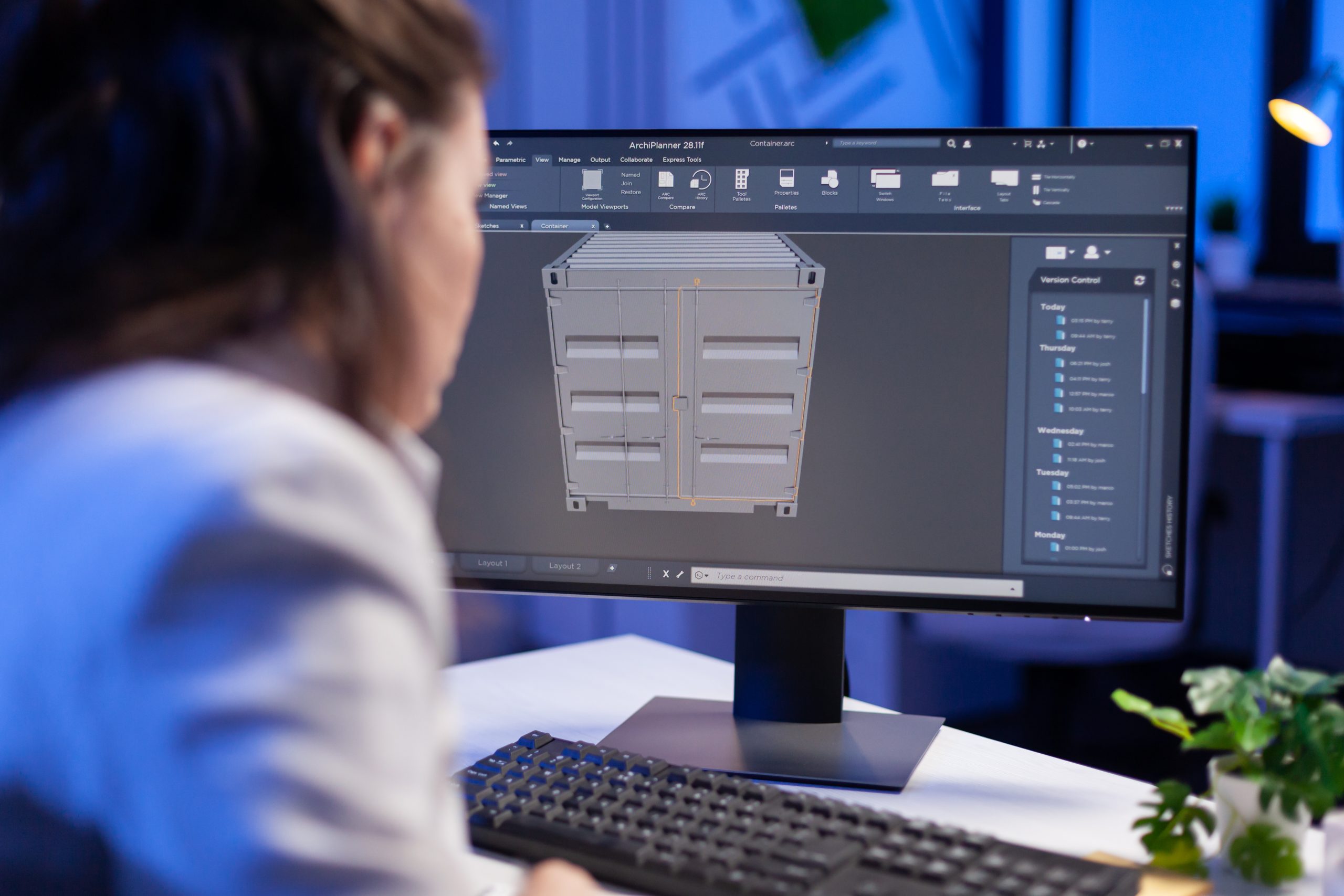
Advanced Mold Design
The design of the mold is another critical factor in producing clear plastic components. The mold must be designed with precision to ensure that the molten plastic flows smoothly and evenly throughout the cavity.
Any inconsistencies in the mold can lead to defects such as flow lines, weld lines, or incomplete filling, all of which can affect the clarity and structural integrity of the final product.
Bosworth Plastics employs advanced mold design techniques to create molds that are perfectly optimised for clear plastic injection molding. Plus, our team of experienced engineers uses state-of-the-art software to simulate the molding process and identify potential issues before the Mold is manufactured.
This proactive approach helps us to minimise the risk of defects and ensure that the final product meets the highest quality control and assurance standards.
Our Precision Standards
Clear plastic injection molding requires precise control over the molding process parameters, including temperature, pressure, and injection speed. These parameters must be carefully calibrated to ensure that the molten plastic fills the mold evenly and without introducing air bubbles or other imperfections.
Temperature control is particularly important, as clear plastics are often more sensitive to temperature variations than opaque materials. If the temperature is too high, the plastic can degrade, leading to yellowing or a reduction in clarity. If the temperature is too low, the plastic may not flow properly, resulting in incomplete filling or surface defects.
At Bosworth Plastics, we use advanced injection molding machines equipped with precise temperature control systems to maintain optimal processing conditions. Our skilled technicians monitor the process closely and make real-time adjustments as needed to ensure the highest quality outcomes.
Post-Production Treatments
Once the clear plastic component has been molded, additional post-production treatments may be necessary to achieve the desired level of clarity and finish. These treatments can include polishing, annealing, or applying coatings to enhance the product’s durability or resistance to UV light.
Polishing is often used to remove any surface imperfections and improve the optical clarity of the product. This can be done mechanically, using buffing wheels or abrasive compounds, or chemically, using solvents or vapour polishing techniques.
Annealing is another important step, particularly for materials like polycarbonate, which can develop internal stresses during the molding process. Annealing involves heating the component to a specific temperature and then cooling it slowly to ensure the material remains stable and clear.
At Bosworth Plastics, we offer a range of post-production services to ensure that our clients receive products that not only meet but exceed their expectations.
Our comprehensive approach to clear plastic injection molding includes everything from material selection and mold design to precision molding and post-production treatments, providing our clients with a complete solution for their clear plastic component needs!
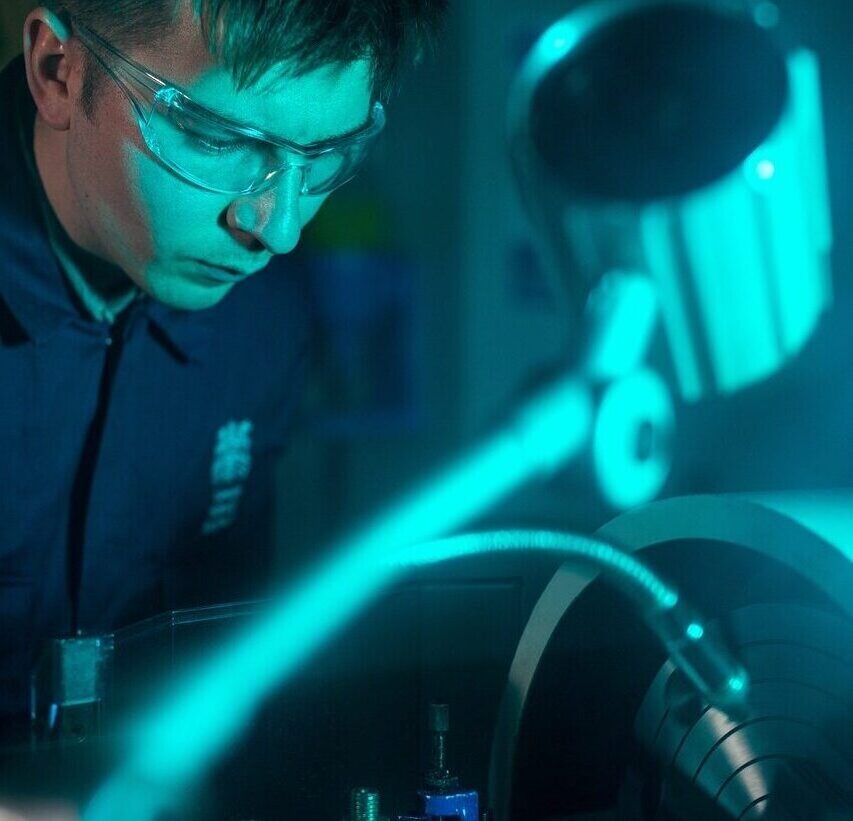
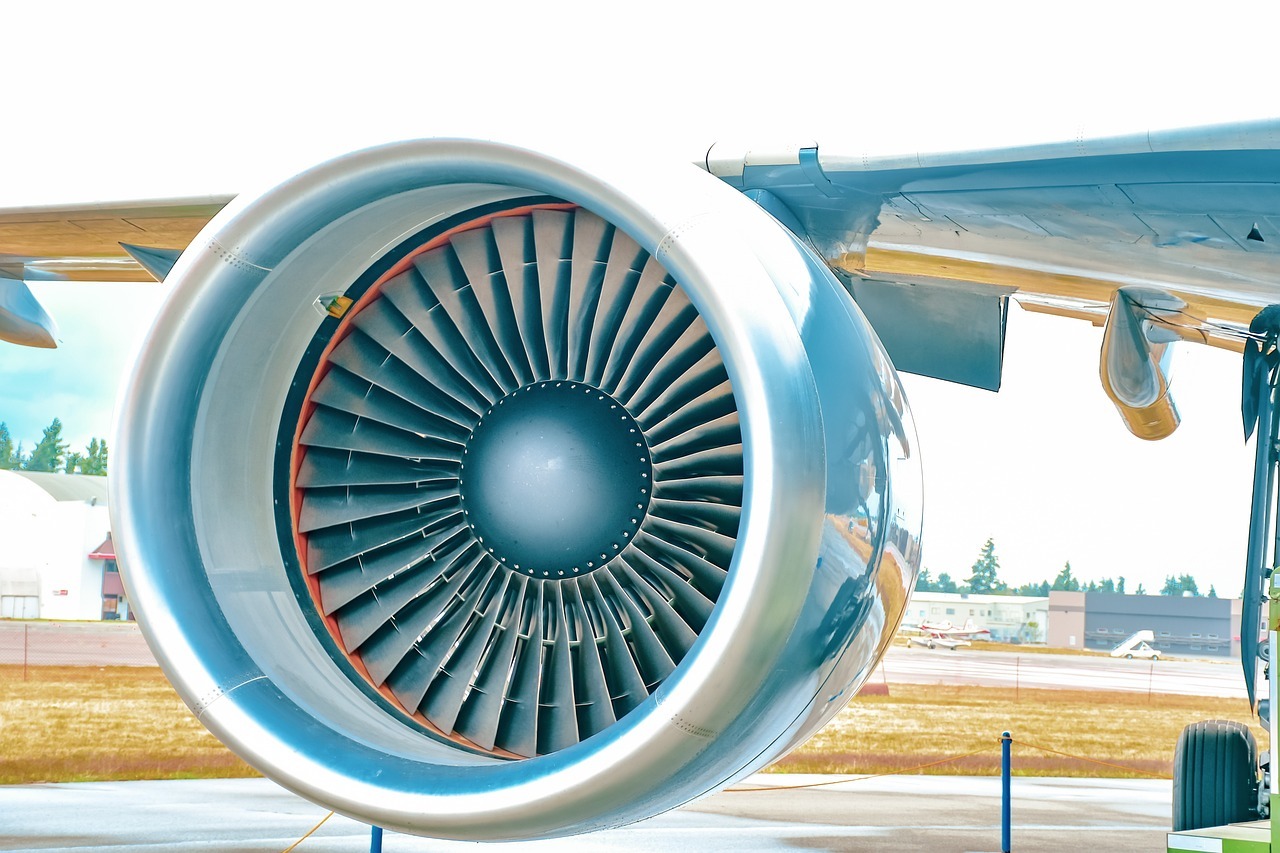

The Common Applications Of Clear Plastic Injection Molding
The versatility of clear plastic injection molding makes it suitable for a wide range of applications across various industries. Some common applications include:
Medical Devices: Clear plastics are widely used in the medical industry for components such as syringes, IV tubes, and diagnostic equipment. The clarity of these components is crucial for ensuring accurate measurements and monitoring.
Automotive Components: In the automotive industry, clear plastics are used for components such as headlamp lenses, instrument panels, and interior trim. The clarity of these parts is essential for both aesthetics and safety.
Consumer Electronics: Clear plastic components are also prevalent in consumer electronics, where they are used for items such as display screens, protective covers, and camera lenses. The clarity and durability of these components are essential for ensuring that the end result is both functional and aesthetically appealing.
Optical Products: Optical products, such as lenses, goggles, and visors, rely heavily on clear plastic injection molding. The precision and clarity of these components are critical for ensuring optimal performance and user safety.
Why Choose Us For Clear Plastic Injection Molding?
Picking Bosworth Plastics as your clear plastic injection molding partner offers several advantages:
Expertise And Experience: With years of experience in the plastics industry, we have developed a deep understanding of the unique challenges associated with clear plastic injection molding. Our team of experts is dedicated to delivering the highest quality products, no matter how complex the project.
State-of-the-art Equipment: We invest in the latest injection molding technology to ensure that our processes are as efficient and precise as possible. Our advanced machinery, combined with our rigorous quality control procedures, allows us to produce clear plastic components with exceptional clarity and consistency.
Customised Solutions: At Bosworth Plastics, we understand that every project is unique. We work closely with our clients to develop customised solutions that meet their specific requirements. Whether you need a small batch of prototypes or a large production run, we have the flexibility and expertise to deliver on time and within budget.
Commitment To Quality: Quality is at the heart of everything we do at Bosworth Plastics. We adhere to strict quality control standards throughout the entire production process, from material selection to final inspection. Our commitment to quality ensures that our clients receive products that are free from defects and meet the highest industry standards.
Sustainability: We are committed to sustainable manufacturing practices and continuously seek ways to reduce our environmental impact. This includes optimising our processes to minimise waste, using energy-efficient equipment, and sourcing materials from suppliers who share our commitment to sustainability.
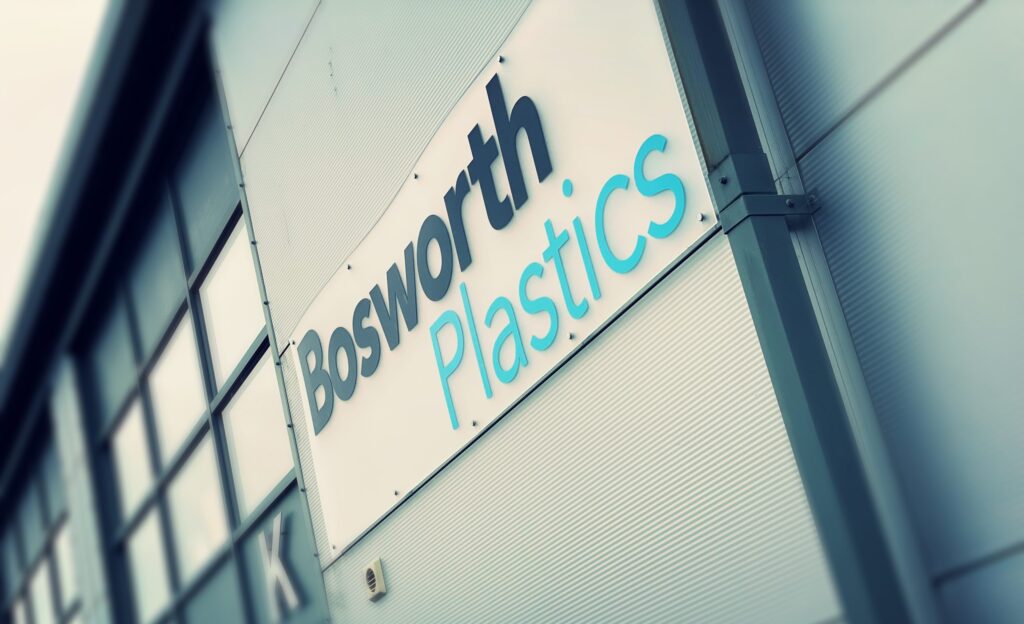
If You’re Looking For Top-Quality Clear Plastic Injection Molding, Make Sure You Contact Us!
Plastic Injection Moulded Product Specialist
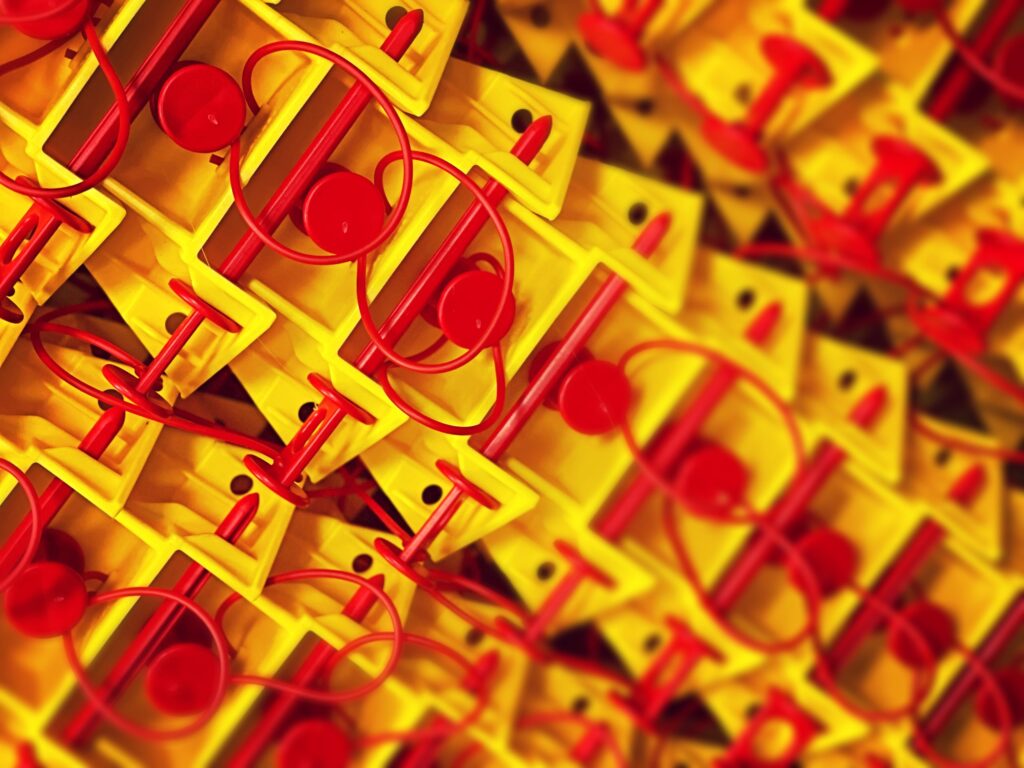
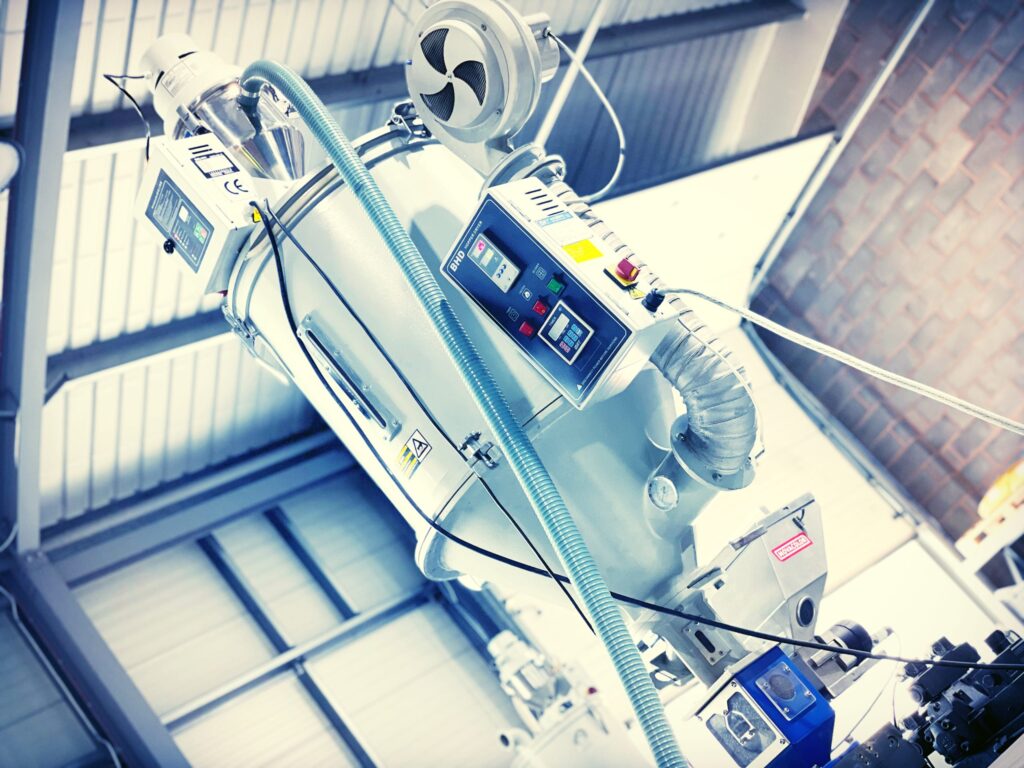
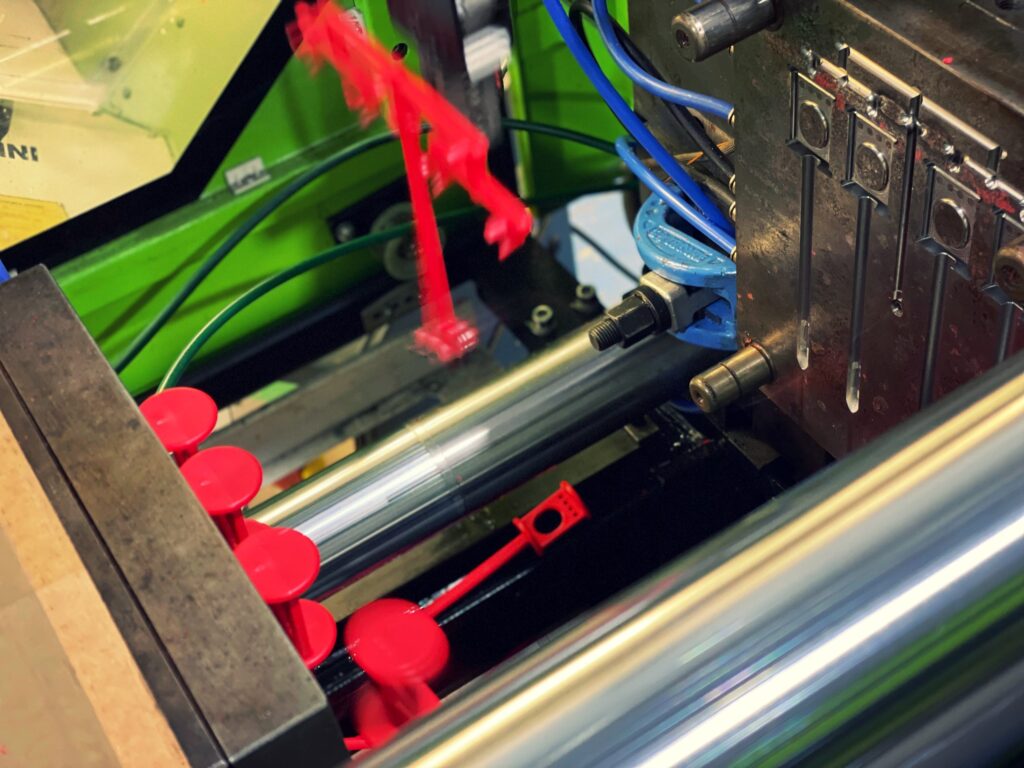
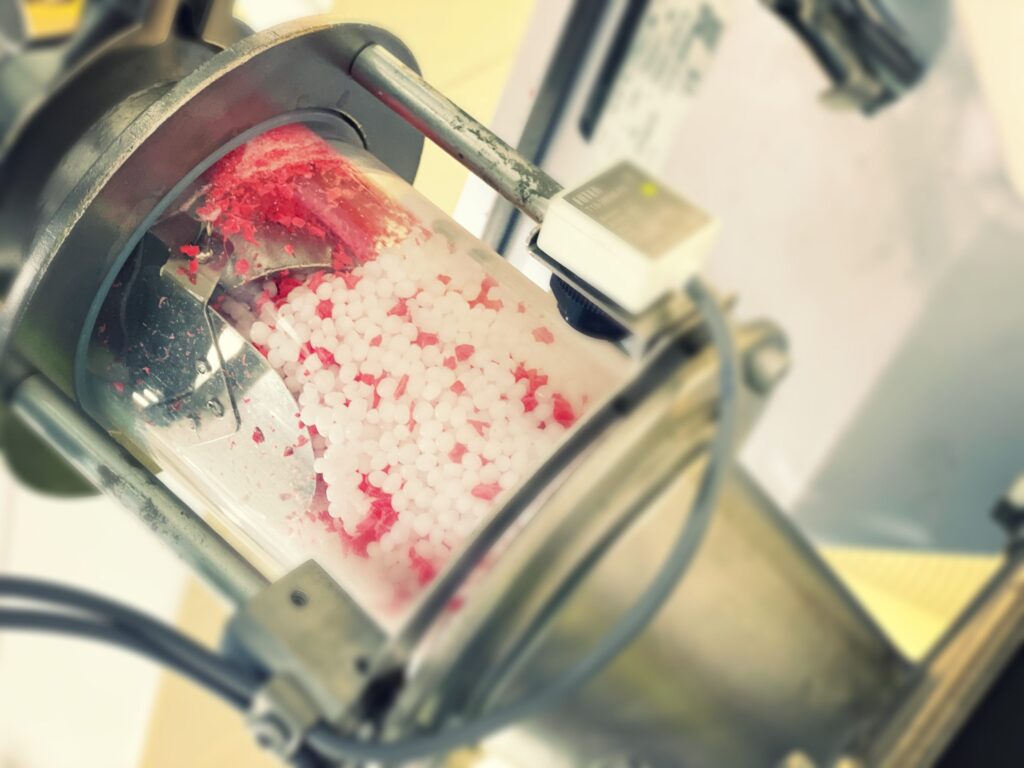